Dosieranlagen
Wir dosieren Chemikalien wo sie gebraucht werden.
Ob in Skidbauweise oder als IBC mit integriertem Pumpenrahmen,
die Anlagen sind äußerst robust und können Zweck und Einsatzort angepasst werden.
Ob in Skidbauweise oder als IBC mit integriertem Pumpenrahmen,
die Anlagen sind äußerst robust und können Zweck und Einsatzort angepasst werden.
Dies bedingt eine Anlagentechnik, die sowohl die Prozessbedingungen in der Hauptanlage, als auch alle erforderlichen Mess- und Regelaufgaben der Dosiertechnik unter Beachtung der erforderlichen Anlagensicherheit, sowie der Arbeitsergonomie berücksichtigt. Daher sind die Dosieranlagen der TBA Thies GmbH & Co. KG meist eine Kombination aus folgenden Baugruppen:
- - Produktvorlage in Kunststoff- oder Edelstahltanks
- - Pumpen, wenn gefordert auch in redundanter Ausführung
- - Anlagenverrohrung in Kunststoff oder Edelstahl mit Drücken bis zu 250 bar
- - Mess- und Regeltechnik
- - Autarke Anlagenregelung oder Aufschaltung auf die Prozessleittechnik
Aufgrund der Vielfalt der Aufgabenstellungen haben wir keine standardisierten Anlagen, sondern konzipieren diese immer gezielt auf den Anwendungsfall.
Kunde: Wintershall Libya
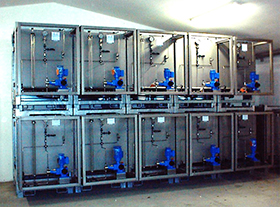
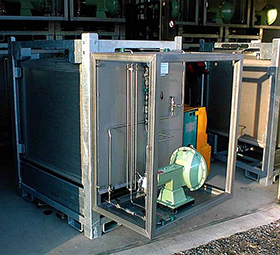
Dosieranlagen für die verschiedensten MedienAuf Basis des Kundenwunsches nach einfach gehaltenen Dosieranlagen für verschiedene Medien wurden diese Dosieranlagen mit minimaler Ausrüstung von uns entwickelt. Sie sind einfach in der Handhabung und es werden vor Ort vier verschiede Medien mit diesen Anlagen dosiert: demulsifier; oxigen scavenger; biozid; corrosion inhibitor.Aufgrund des kompakten und einfachen Designs bieten sie eine hohe Flexibilität bei starker Kosteneffizienz. Durch die stapelbare Ausführung sind sie zudem besonders platzsparend in der Vorratshaltung. Seit 2002 sind 150 Anlagen an den Bohrplätzen in Betrieb genommen worden.
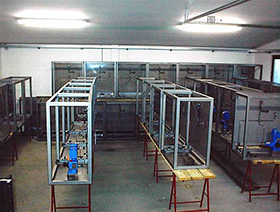
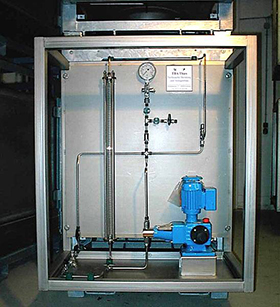
Kunde: Wintershall Barnstorf
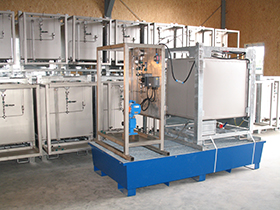
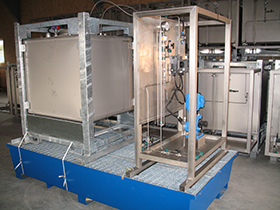
Dosieranlage mit mobilem VorlagetankDas Medium wird mittels der Dosierpumpe zur Injektionsstelle gefördert. Der Vorlagebehälter wird zur Befüllung zum Umfüllplatz gebracht und nachfolgend wieder eingesetzt. Hierfür mussten alle Rohrleitungen, sowie die Kabelverbindungen zu den Sicherheitseinrichtungen trennbar ausgeführt werden, was im Ex-Bereich nur mit eigensicheren Komponenten sicher umzusetzen ist.Aus Kostengründen wurde für die Auffangwanne eine Standardauffangwanne gewählt. Geringe Anforderungen hinsichtlich der Medienbeständigkeit ermöglichten die Ausführung mit einer kostengünstige Standardauffangwanne, hier als beschichtete Stahlwanne.
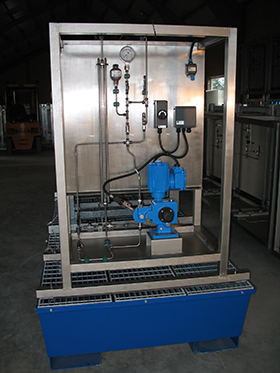
Kunde: Wintershall Barnstorf
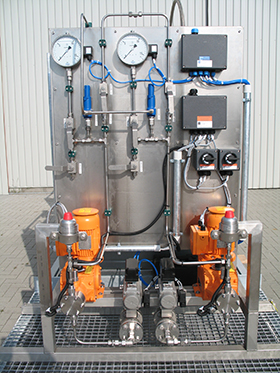
Dosieranlage mit redundanter PumptechnikDas Medium fließt vom höhergelegenen Wechsel-IBC in die tiefergelegene Vorlage. Von dieser wird es mittels der Dosierpumpe zur Injektionsstelle gefördert. Die Dosierstränge sind durch elektropneumatisch angetriebene Kugelhähne umschaltbar. Durch die Gaspendelleitung wird gewährleistet, dass lediglich eine minimale Emission des hochgiftigen Mediums in die Umwelt entweicht.Als Sicherheitsabschaltung sind die Manometer mit Grenzkontakten ausgestattet. Die Elektrotechnik ist für Ex-Zone 2 konzipiert.Die Auffangwanne ist nach WHG für das maximal mögliche Behältervolumen ausgeführt.

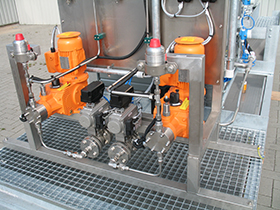
Kunde: RWE Dea Nile Branch, Egypt
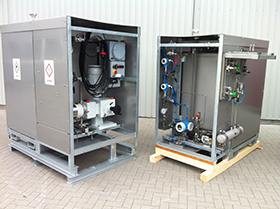
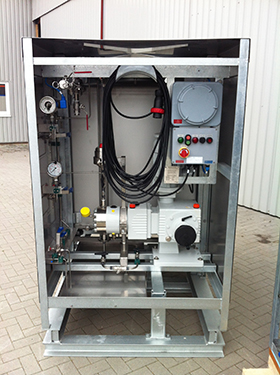
Dosierung von Methanol und Corrosion InhibitorAuf Basis einer internationalen Ausschreibung erhielt die TBA Thies GmbH & Co. KG den Auftrag zum Bau von drei Methanol-Dosieranlagen sowie 15 Dosieranlagen für Corrosion Inhibitor (Bild oben links und rechts). Die Anlagen sind auf Erdgasfeldern in ägypten eingesetzt.Die Methanol-Dosieranlagen (Bild unten links) fördern gegen einen Leitungsdruck von bis zu 300 bar mit einem Volumenstrom von bis zu 110 l/h. Auf Kundenwunsch wurden LEWA-Pumpen mit manueller Hubverstellung eingesetzt. Die lokale Steuerung sichert mit der montierten Sensorik einen funktionssicheren Betrieb in der Ex-Zone 2.Bei den Corrosion Inhibitor – Dosieranlagen wurde ebenfalls besonderen Wert auf die Anlagensicherheit gelegt. Diese Anlagen laufen ohne Aufsichtspersonal, so dass sie zusätzlich mit redundanter Drucküberwachung und einer Coriolis-Durchflussmessung ausgerüstet wurden. (Bild mittig rechts) Da vor Ort kein Strom für den Antrieb der Pumpen zur Verfügung gestellt werden konnte, wurde das Erdgas als Antriebsmittel eingesetzt. Da es mit einem Druck von bis zu 90 bar hinter den HIPPS abgegriffen wird, ist eine umfangreiche Druckreduzierung mit Zwischenerwärmung vorgesehen (Bild unten rechts).
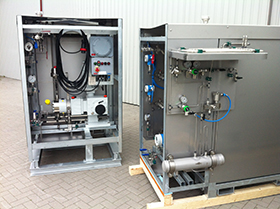
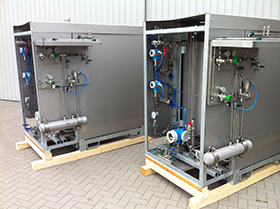
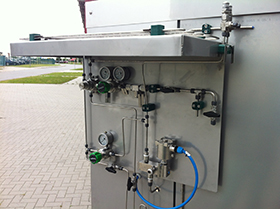